Polishing: Revealing the Soul of the Blade
Once a sword blade is forged and shaped, it is entrusted to a professional polisher, known as a togishi. Polishing is a highly intricate and specialized art that plays a critical role in bringing out the blade’s true character and beauty.
The polishing process involves multiple stages using whetstones of varying grit, progressing from coarse to fine. The ultimate goal is to achieve a flawless, mirror-like surface that highlights the hamon (temper line) and other distinctive features of the blade.
Though polishing does not demand the intense physical strength required for forging, it is still a physically demanding task. Togishi must maintain an awkward kneeling posture for extended periods, often working with freezing cold blades and water, especially in winter.
The Tools of Polishing: Understanding Grit and Technique
Each whetstone is categorized by its grit number—the higher the number, the finer the grit. The polishing process generally consists of two stages: rough polishing and fine polishing.
Rough Polishing (Shitaji Togi)
Rough polishing uses larger and coarser stones to shape and sharpen the blade:
-
Kongo-do (180 grit)
Made from natural coarse sandstone or artificial carborundum, this stone removes vertical hammer marks, sharpens the edge, and forms the blade ridge. The blade is kept perpendicular to the stone.
-
Beshui-do (280–320 grit)
Slightly finer sandstone. Here, the blade is angled slightly to distinguish new scratch marks from previous ones.
-
Kaisei-do (400–600 grit)
A further refinement stage, where the blade’s surface becomes smoother, darker, and more reflective. The hamon starts to appear faintly.
-
Nakato-do (800–1500 grit)
Divided into medium (800 grit) and fine (1200–1500 grit) stones. During this stage, the blade is no longer fixed at a strict angle but is slightly rocked during polishing to refine the details.
-
Uchigumori (3000 grit and above)
At this stage, only natural stones are used. Stones are extremely fine, and any flaw in the stone could scratch the blade irreparably. Uchigumori is divided into medium and fine grades, used to further clarify the hamon and remove previous scratch patterns.
After the uchigumori stage, the blade is already razor-sharp. Further fine polishing is mainly for aesthetic purposes—to enhance surface reflections and display intricate steel structures.
Fine Polishing (Shiage Togi)
Fine polishing employs extremely thin pieces of natural stones, resembling paper in thickness. Using only the thumb for pressure, the polisher brings out the finest details of the hamon, nioi (temper mist), nie (martensitic crystals), and utsuri (shadow patterns).
Key steps include:
-
Yaiba (Arrowtail Polishing)
Thin slices of uchigumori are used to eliminate any remaining scratches from the previous steps.
-
Ji-e and Ha-e Polishing
- Ji-e stones (yellow-brown or orange) deepen the color of the blade’s surface and reveal the grain pattern (jihada).
- Ha-e stones (light gray) focus on enhancing the blade edge.
-
Wiping with Magnetite Suspension
A fine suspension of magnetite in clove oil is applied with cotton to darken the surface, accentuating the steel’s patterns. Overuse can overly darken the blade.
-
Migaki-bo (Polishing Rod)
A metal rod is used to further polish the mune (back ridge) and shinogi-ji (blade flats), giving them a true mirror finish.
-
Hadori (Edge Work)
Hadori is one of the most delicate and artistic stages in the sword polishing process, aimed at refining and visually enhancing the hamon (temper line) of the blade.
During hadori, the polisher cuts thin slices of fine-grit ha-e stones into small elliptical shapes. These custom-shaped stone pieces allow for meticulous control. Using only their fingers to apply subtle pressure, the polisher gently follows the flow of the hamon, adjusting and redrawing its shape to achieve a more aesthetically ideal form.
The purpose of hadori is to emphasize the contrast between the cutting edge and the body of the blade, resulting in a whiter, non-reflective hamon set against the polished surface.
Unlike fake hamon on mass-produced blades, hadori builds upon the authentic natural hamon, enhancing but not fabricating its beauty. It is makeup, not plastic surgery.
For straight hamon (suguha), the cosmetic and real hamon align perfectly. For irregular patterns (midareba) with intricate features like ashi, hadori may slightly generalize the details without altering the overall integrity.
Polishing highlights material differences: pearlite structures within the ashi appear brighter than the surrounding martensitic steel, enriching the visual depth of the blade.
Ultimately, hadori reflects the polisher’s mastery and deep interpretation of the blade’s spirit, elevating the sword into a true work of art.
It is worth noting that if a sword features grooves (hi) or carvings (horimono), the polishing process becomes even more complex and time-consuming.
Test Cutting: Proof of Performance
After the sword is polished and completed, it may undergo tameshigiri, or test cutting, to verify its sharpness and resilience.
Historically, the targets were cadavers or condemned criminals. Successfully cutting through one body was called “ichidō” (one torso), two bodies were “nidō”, and so on. The record for test cutting was achieved by the samurai Nakagawa Jūrobē at the age of 68, using a blade forged by Kanefusa—successfully cutting through seven bodies in one stroke (“shichidō”).
Today, using human targets is considered barbaric. Modern test cutting, called aratameshi or katamono-shi, uses hard objects like armor to evaluate the blade’s performance. Contemporary masters like Yoshihara Yoshindo still value and practice test cutting to assess the true capability of their swords.
The Art Behind the Katana
The artistry behind polishing and testing a Japanese sword reveals the true spirit of craftsmanship. It is not merely a technical process but a deep tradition that honors the blade’s soul, ensuring each katana achieves its maximum beauty and performance.
Read more
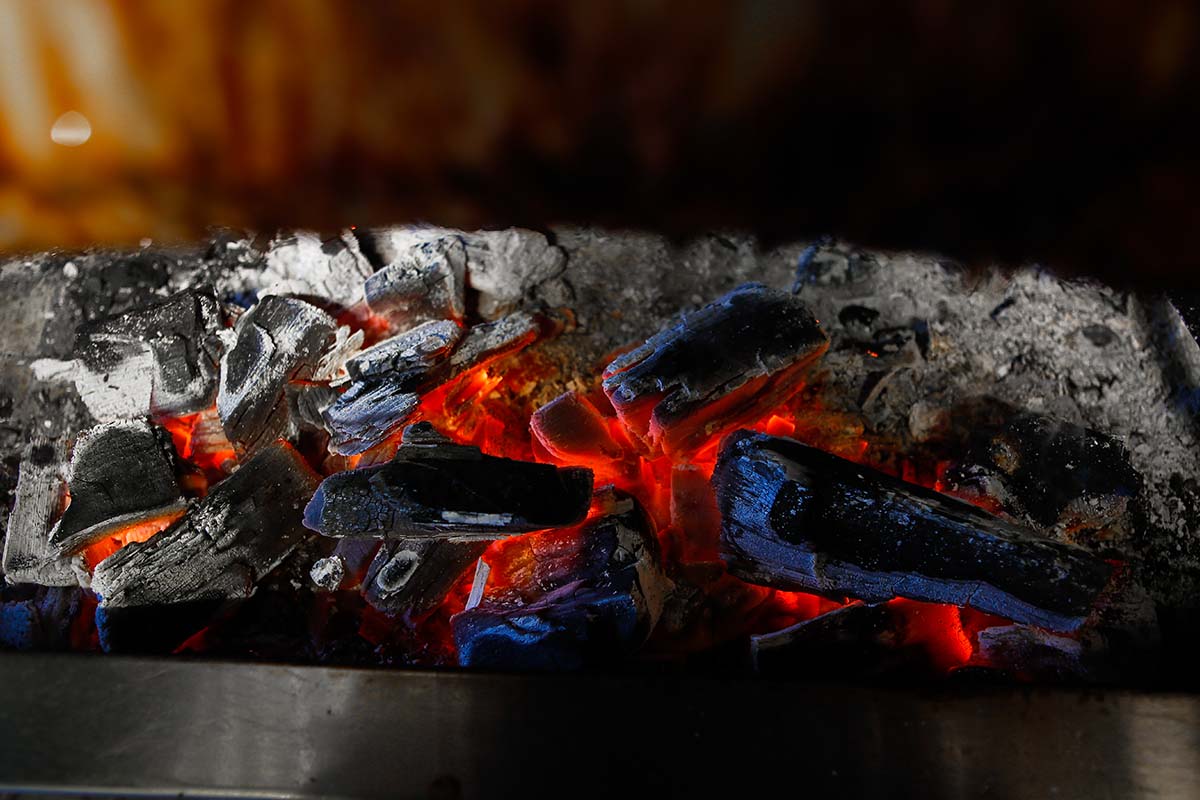
Tamahagane, the legendary steel behind authentic Japanese katanas, is forged through a centuries-old tradition using iron sand and charcoal. Discover the intricate smelting process inside the ancie...
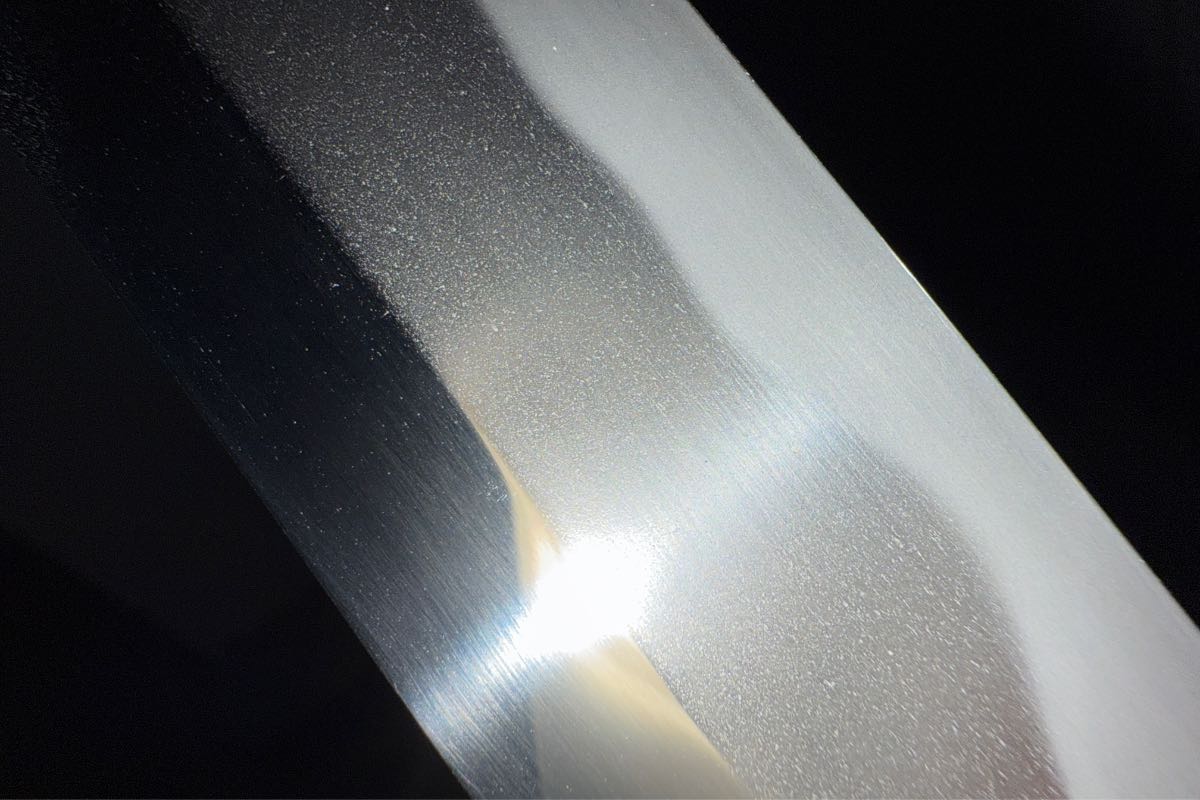
Discover how the quenching process creates the stunning beauty of nioi and nie in Japanese swords. Learn about rare features like sunagashi, kinsuji, utsuri, and the hidden secrets of traditional f...
Shop katana
Our katana store offers a wide selection of japanese swords — from traditional katanas and anime-inspired designs to fully functional blades — featuring a variety of materials and craftsmanship to suit your preferences.
Leave a comment
All comments are moderated before being published.
This site is protected by hCaptcha and the hCaptcha Privacy Policy and Terms of Service apply.